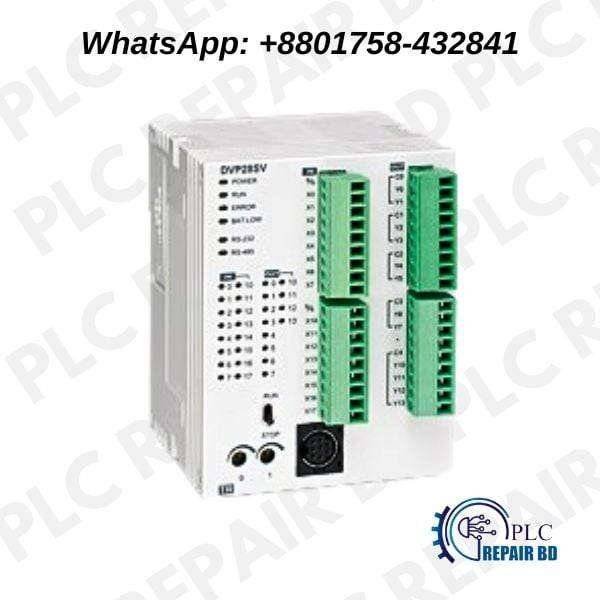
Introduction
If you’re seeking reliable Delta PLC repair services in Bangladesh, look no further. We specialize in providing top-notch repair and maintenance solutions for Delta programmable logic controllers (PLCs). With a team of highly skilled technicians and a commitment to excellence, we ensure that your industrial automation systems remain in optimal condition, minimizing downtime and maximizing productivity.
Whether it’s troubleshooting, component replacement, or software upgrades, we’re your trusted partner in keeping your Delta PLCs running smoothly. Count on us for efficient, cost-effective, and timely PLC repair services tailored to your specific needs. Your success is our priority.
Our PLC Repair Service Area
Our repair services cover a wide service area throughout Bangladesh. We are committed to providing reliable, efficient, and cost-effective repair solutions to businesses across the country. Our service area encompasses major cities, industrial zones, and regions to ensure that clients in various industries have easy access to our expertise.
What problems do we solve for PLC Repair?
- Power Supply Issues: Problems with the power supply, such as voltage fluctuations, electrical surges, or inadequate power, can lead to hardware malfunctions.
- Faulty Input/Output (I/O) Modules: Defective input or output modules can disrupt communication between the PLC and external devices, leading to errors in controlling machinery or processes.
- CPU Failure: The central processing unit (CPU) is the heart of the PLC. Any failure or damage to the CPU can result in a complete system breakdown.
- Memory Errors: Issues with memory modules, including corrupted or damaged memory chips, can lead to data loss or program execution errors.
- Communication Problems: Hardware-related communication issues, such as damaged communication ports or network interfaces, can disrupt data exchange with other devices or systems.
- Environmental Factors: PLC hardware can be sensitive to environmental factors like extreme temperatures, humidity, or dust. Exposure to these conditions can cause hardware failures over time.
- Physical Damage: Mechanical damage, like impacts, vibration, or exposure to contaminants, can harm the hardware components, including connectors, cables, and circuit boards.
- Wear and Tear: Over time, components like relays, connectors, and power supplies may degrade due to normal wear and tear, leading to failures.
- Component Aging: Like any electronic device, PLCs can suffer from component aging, where components like capacitors may lose their effectiveness over time.
- Incompatibility: Using incompatible or outdated hardware components can result in system instability and hardware problems.
We provide PLC repair services of any brand. For example:
Siemens PLCs:
- Siemens S7-1200 series
- Siemens S7-1500 series
- Siemens S7-300 series
- Siemens S7-400 series
Allen-Bradley (Rockwell Automation) PLCs:
- Allen-Bradley MicroLogix series
- Allen-Bradley CompactLogix series
- Allen-Bradley ControlLogix series
- Allen-Bradley PLC-5 series
Mitsubishi Electric PLCs:
- Mitsubishi MELSEC FX series
- Mitsubishi MELSEC L series
- Mitsubishi MELSEC Q series
- Mitsubishi MELSEC iQ-F series
ABB PLCs:
- ABB AC500 series
- ABB AC800M series
- ABB AC500-eCo series
Omron PLCs:
- Omron CP1E series
- Omron CP1L series
- Omron CP1H series
- Omron CJ2M series
Delta Electronics PLCs:
- Delta DVP-EH2 series
- Delta DVP-ES2 series
- Delta DVP-SS2 series
- Delta DVP-SX2 series
Schneider Electric PLCs:
- Schneider Electric Modicon M340 series
- Schneider Electric Modicon M580 series
- Schneider Electric Modicon Premium series
Beckhoff PLCs:
- Beckhoff TwinCAT series
- GE Fanuc PLCs:
- GE Fanuc Series 90-30
- GE Fanuc Series 90-70
Hitachi PLCs:
- Hitachi H series
- Hitachi EH series
Fuji Electric PLCs:
- Fuji Electric MICREX-SX series
Panasonic PLCs:
- Panasonic FPX series
Understanding Delta PLC Repair Services in Bangladesh
DVP-SV2 Series, DVP-SX2 Series, DVP-SX Series, DVP-SA2 Series, DVP-SE Series, DVP-SS2 Series. Delta Programmable Logic Controllers (PLCs) are widely used in industries across Bangladesh, powering various automation processes. However, like any complex electronic system, Delta PLCs can encounter issues and faults over time. To address these problems effectively, it’s crucial to understand common issues and consider essential factors when choosing a Delta PLC repair service provider.
Common Issues and Faults Encountered with Delta PLC Systems
Communication Failures: Delta PLCs often interface with other equipment and systems. Communication failures, such as problems with Ethernet, RS-232, or RS-485 connections, can disrupt data exchange and control processes.
- Faulty Inputs/Outputs: Issues with digital and analog inputs/outputs can lead to incorrect readings or unreliable control, impacting the overall system’s performance.
- Power Supply Problems: Delta PLCs require a stable power supply. Voltage fluctuations or power surges can damage the PLC or cause erratic behavior.
- Software Errors: Programming errors, incorrect logic, or outdated firmware can lead to system malfunctions. Skilled technicians are needed to debug and reprogram the PLC.
- Overheating and Environmental Damage: PLCs exposed to harsh industrial environments may suffer from overheating or physical damage. Regular maintenance is necessary to prevent these issues.
- Component Failures: Components like CPUs, memory units, and communication modules can fail due to wear and tear. Replacing these components requires expertise and access to genuine parts.
Key Factors to Consider When Choosing a Delta PLC Repair Service Provider
- Expertise and Experience: Look for service providers with a proven track record of working with Delta PLCs. Experience matters, as it indicates their ability to diagnose and resolve issues efficiently.
- Technical Skills: Ensure that technicians possess the technical skills and certifications necessary for Delta PLC repairs. Delta-certified technicians have specialized knowledge that can be invaluable.
- Availability of Genuine Parts: A reputable service provider should have access to genuine Delta PLC spare parts. Using counterfeit or incompatible components can worsen the problem.
- Turnaround Time: Take into account how quickly the service provider can complete repairs. Fast and efficient service minimizes downtime and reduces production losses.
- Customer Support: Excellent customer support is crucial. The provider should offer ongoing assistance, troubleshooting help, and preventive maintenance advice.
- Pricing and Transparency: Compare pricing structures and ensure transparency in the cost breakdown. Exercise caution when encountering service providers who quote significantly lower prices, as this could potentially signify a lower quality of service.
- Reputation: Research the provider’s reputation through reviews, referrals, and testimonials from other businesses. A favorable reputation serves as a robust signal of trustworthiness.
- Compliance and Certifications: Verify that the service provider complies with industry standards and holds necessary certifications. This ensures quality work and adherence to safety guidelines.
- Warranty and Guarantees: Inquire about warranties or guarantees on their repairs. A provider willing to stand behind their work demonstrates confidence in their service quality.
Selecting the Right Delta PLC Repair Service Provider
Once you have compared service providers based on the above factors, it’s time to make an informed decision. Here are some additional considerations:
Assessing Individual Business Requirements and Specific Needs
Each business has unique requirements and specific needs when it comes to Delta PLC repairs. It’s essential to assess these needs comprehensively and choose a service provider who can tailor their services to align with your business goals.
Quality of Repairs and Reliability
The quality of repairs should never be compromised. Choose a service provider with a track record of delivering reliable and long-lasting repairs. High-quality work ensures that your PLCs operate smoothly, reducing the likelihood of future breakdowns.
Reputation and Track Record of the Service Provider
Reputation matters. Seek out service providers with a strong track record of customer satisfaction and positive reviews from other businesses in your industry. A trusted partner is more likely to deliver on their promises.
Cost-Effectiveness and Value for Money
While cost plays a role, it should not be the exclusive determining factor. Instead, focus on value for money. A service provider that offers a comprehensive package, including excellent service quality and support, may be a more cost-effective choice in the long run.
Leading Delta PLC Repair Service Providers in Bangladesh
When it comes to Delta PLC repair service providers in Bangladesh, two companies stand out for their expertise, experience, and specialization in delivering top-notch repairs for Delta PLCs. Let’s take a closer look at what makes Company A and Company B leaders in this field.
Company A: Expertise, Experience, and Specialization in Delta PLC Repairs
1. Range of Services Offered
Company A has earned its reputation through its extensive range of services tailored specifically for Delta PLCs. They offer comprehensive solutions that cover troubleshooting, diagnostics, maintenance, and repairs. Whether you need a quick fix or a complete overhaul, Company A has you covered.
2. Client Testimonials and Feedback
The true measure of a service provider’s quality is the feedback from satisfied clients. Company A boasts a long list of client testimonials, highlighting their exceptional work in Delta PLC repairs. These testimonials speak volumes about the reliability and trustworthiness of Company A’s services.
Extensive Knowledge of Delta PLC and Success Stories in Repairs
Garnered a reputation for its in-depth knowledge of Delta PLCs and a string of success stories in repairs. Here’s what sets them a part:
1. In-Depth Knowledge
Company B’s technicians possess a deep understanding of Delta PLCs, which allows them to diagnose issues quickly and accurately. Their expertise extends beyond routine repairs, enabling them to tackle even the most complex problems with precision.
2. Success Stories in Repairs
Company B has a track record of successfully resolving challenging Delta PLC issues. They have turned around situations where other providers have failed, earning the trust of clients who value effective solutions and minimal downtime.
Comparing Delta PLC Repair Service Providers in Bangladesh
In the world of industrial automation, Delta Programmable Logic Controllers (PLCs) have become an integral component for countless businesses across Bangladesh. These devices play a pivotal role in ensuring the seamless operation of manufacturing processes, making their maintenance and repair critical to business continuity. However, choosing the right Delta PLC repair service provider can be a daunting task. To simplify this decision-making process, it’s essential to consider several key factors.
Pricing and Service Packages Offered
One of the primary factors to evaluate when comparing Delta PLC repair service providers in Bangladesh is their pricing structure and the service packages they offer. Businesses should seek transparent pricing models that align with their budgets while ensuring that critical services are not compromised. A well-defined service package should encompass not only repairs but also preventative maintenance and troubleshooting support.
Turnaround Time for Repairs
Downtime in industrial settings can be costly. Therefore, the turnaround time for repairs is of paramount importance. A reputable service provider should have efficient processes in place to diagnose and repair Delta PLCs swiftly. This ensures minimal disruption to production schedules, enhancing overall operational efficiency.
Availability of Spare Parts and Component Sourcing
Timely access to genuine spare parts and components is another crucial aspect to consider. Service providers with well-established supply chains and access to Delta-approved spare parts can ensure that repairs are carried out with the highest quality components, reducing the risk of recurrent issues.
Customer Support and After-Repair Services
Exceptional customer support is the cornerstone of a reliable PLC repair service provider. Businesses should look for providers who offer ongoing technical support and after-repair services. This includes assistance with programming, troubleshooting, and guidance on preventive measures to prolong the PLC’s lifespan.
Conclusion
when it comes to Delta PLC repair services in Bangladesh, our expertise and commitment to excellence make us your trusted partner in ensuring the uninterrupted operation of your industrial automation systems.
Other Equipment We Repair
Siemens plc repair | Mitsubishi plc Repair | Omron PLC Repair
Contact Information:
Phone: +8801758432841
Email: plcrepairbd@gmail.com
Address: House-29, Road-1, Nikunja-2, Khilkhet, Dhaka-1229.
Frequently Asked Questions: Delta plc repair services in Bangladesh
What is a PLC, and why would it need repair?
A Programmable Logic Controller (PLC) is a device used in industrial automation to control machinery and processes. PLCs can require repair due to wear and tear, component failures, or software issues that can affect their functionality.
What brands and models of Delta PLCs do you repair?
We offer repair services for a wide range of Delta PLCs, including popular models such as Delta DVP series, Delta EH3 series, Delta SS2 series, and many others.
How do I know if my Delta PLC needs repair?
Common signs include system errors, erratic behavior, communication problems, or hardware component failures. If you suspect an issue with your Delta PLC, it’s advisable to consult a professional technician for diagnosis.
Do you provide on-site repairs, or do I need to send my PLC to your facility?
Our services include both on-site and off-site repairs, depending on the nature of the problem and your location. We can assess the situation and recommend the most suitable approach.
What is the typical turnaround time for PLC repairs?
Turnaround times can vary depending on the complexity of the issue and the availability of replacement parts. We strive to provide fast and efficient service to minimize downtime.
Do you offer warranty for your PLC repair services?
Yes, we typically provide a warranty on the repairs performed and any replacement parts used. This warranty can vary in duration, so be sure to inquire about the specific terms.
CONTACT US